EV Battery technologies – staying ahead of the pack
20.03.2024
The switch to electric mobility is gathering pace and as energy technologies become more advanced, so do the challenges for vehicle manufacturers. For example, silencing efforts have shifted from the powertrain to road and wind noise, while batteries have specific needs in terms of thermal management. As a long-established partner of the automotive sector, we are committed to giving our customers what they need to stay ahead.
The value of experience in an evolving industry
Carpenter has been investigating and developing solutions for batteries since the early days of electromobility and has extensive knowledge of the technologies as well as market trends. A key consideration in today’s industry is the lack of standardisation. Battery design is still evolving to increase energy density and lifetime, reduce costs and shorten charging times. And as battery technologies develop, so do the demands on every component within and around the battery pack.
The breadth of our materials portfolio and processing capabilities adds significant value in this regard. Our materials range spans foams (PU, PE, EPDM, silicone), facings (PU film, non-woven, etc.), fibres (PET, PU, etc.) and adhesives. We are also highly experienced in combining these to achieve specific results, applying advanced in-house processing capabilities in cutting, lamination, spooling and thermocompression.
This gives our engineers the flexibility to develop solutions quickly and meet new needs as they emerge. In the absence of industry standards for battery design, we take a tailored approach, differentiating on the basis of battery cell chemistry, design, format, integration and thermal control technology.
The main components of an EV battery
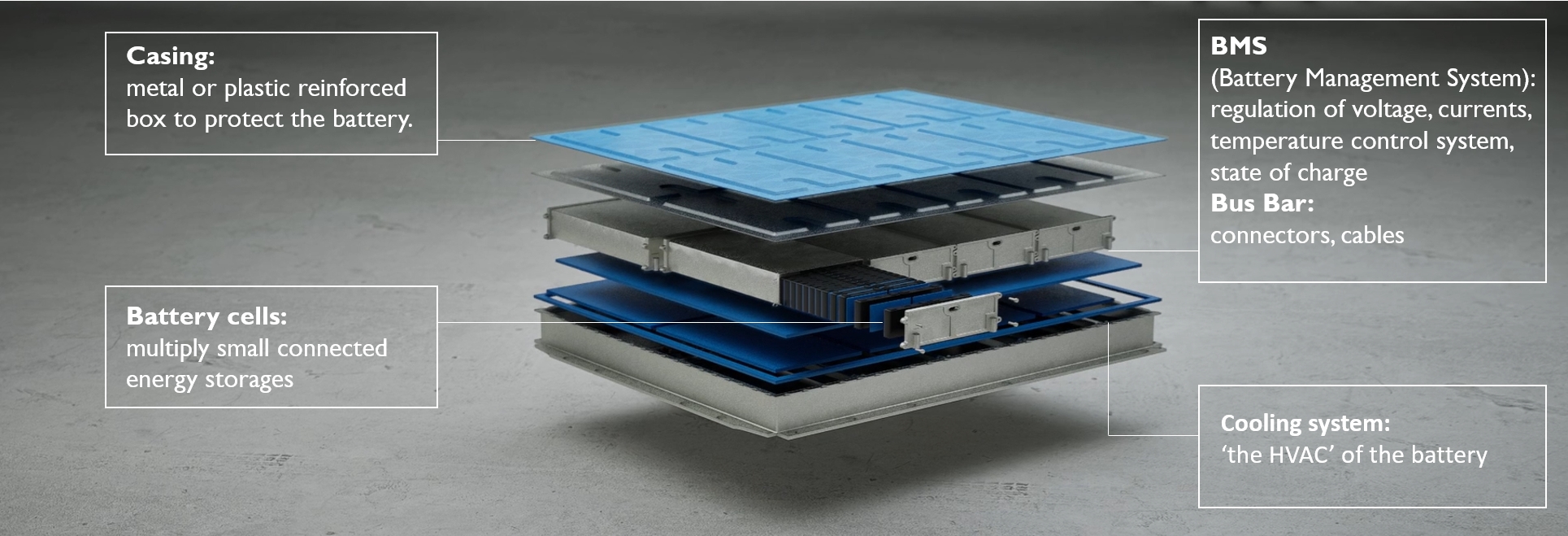
The battery pack: an extreme environment
From full plug-in battery electric vehicles (BEV) to different hybrid variants (PHEV, HEV and MHEV), all electric vehicles have one requirement in common. The battery cell and pack need protection that can withstand extreme conditions. The challenges include heat, expansion and contraction created by the electrical current inside the battery cell, and thermal runaway. The optimal temperature for battery cell performance is 40°C, and materials used in the battery pack must be able to work with the manufacturer’s cooling systems for the most efficient thermal management.
A portfolio dedicated to EV batteries
As well as thermal control solutions for every cooling system, we provide purpose-designed pads and materials to protect, seal and thermally insulate the battery cells and battery pack. Our Carryopt product lines are engineered for optimal carrying and support of battery components. They are available in different variants to meet specific requirements in terms of hardness, compression set, electrical resistance, flame behaviour, vibration isolation, price/performance ratio and more.
Creating the future of mobility
In addition to EV battery applications, we support manufacturers with forward-thinking solutions for: electric motor encapsulation, HVAC sealing and insulation, power inverter insulation, side fender seals, silent tyre and wheel arch acoustic pads.
Our engineers love a challenge!
Contact us to discuss specific requirements for your innovations.